BullX Team - Introduction
BullX Team has over 40 years of combined experience in hydrogen technologies, specializing in fuel cells and electrolysis. They offer expertise in research and development, scale-up, and commercialization, as well as process development and modeling. Their facilities provide machining and prototyping capabilities, computational modeling, and test facilities for fuel cell and electrolysis systems.
- BullX Team
- hydrogen technologies
- fuel cells
- electrolysis
- research and development
- scale-up
- commercialization
- process development
Download Presentation
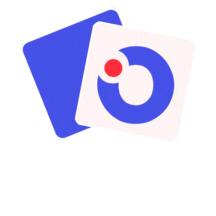
Please find below an Image/Link to download the presentation.
The content on the website is provided AS IS for your information and personal use only. It may not be sold, licensed, or shared on other websites without obtaining consent from the author. Download presentation by click this link. If you encounter any issues during the download, it is possible that the publisher has removed the file from their server.
E N D
Presentation Transcript
Introduction BullX Team
Team introduction Team introduction Over 40 years combined experience in hydrogen technologies including fuel cells and electrolysis. Experience heavily focused on research and development, scale-up and commercialization. Process development, process modeling, PFD, P&ID, equipment and instrumentation specification and selection, HAZOP, FMEA, start-up and commissioning of fuel cell and electrolysis prototypes, pilot and commercial systems Automated state of health monitoring and SCADA integration and operation of fuel cell and electrolysis plants Electrochemical cell and stack development, model driven design (CFD, FEA) Experience in PEM, MCFC, SOFC and PAFC fuel cell systems Experience in PEM, Alkaline-water and SOEC electrolysis systems Experience conducting market research, technical and economic feasibility, technical due diligence for investment
Facilities and Capabilities Facilities and Capabilities Machining and prototyping capabilities Lathe, CNC, 3-D printing, laser cutting and other fabrication methods Computation and modeling CAD, CAM Computational fluid dynamics Stress analysis Process modeling Electrochemical modeling Custom scripting and code generation Test facilities R&D electrochemical characterization Lab scale test and conditioning facilities for fuel cell and electrolysis systems 200-kW generation facility for electrolysis test and conditioning
Electrolyzer Electrolyzer development development Alkaline-Water Electrolysis Extensible to other chemistries and electrolysis technologies Designed from the ground up for manufacturability Low capital and maintenance cost design High potential for production scaling Targeting a highly automated process Scaling to MW+ production rates should be straight forward with GW scaling easily possible depending on finance Patent pending technologies First prototype proving out production methods - expected March 2023
IEA Electrolyzer Analysis Almost 1 GW of installed hydrogen electrolyzer capacity worldwide. Estimated installed capacity would spike to 134-240 GW if all existing projects in the pipeline come to fruition. This number of announced projects has double year over year. IEA expects global electrolyzer production capacity to double to nearly (only) 8 GW total. However, electrolysis capacity is growing from a very low base and requires a significant acceleration to get on track with the Net Zero Emissions by 2050 Scenario, which requires expanding electrolysis capacity to above 700GW by 2030. IEA does not account for replacement of failed or aged out electrolyzer stacks
Market Trends for Electrolysis Systems Total installed electrolysis capacity by technology in the Net Zero Scenario, 2019-2030 (IEA) Other/u nknown MW Alkaline MW PEM MW Total MW Year If all the projects currently in the pipeline are realised, global electrolysis capacity could reach 134-240 GW in 2030. Europe and Australia lead the scene, with about 30% of the capacity each, followed by Latin America with more than 10% of the announced projects. (IEA report) 2019 164 65 13 242 2020 197 93 14 304 2021 354 126 33 513 2022 727 366 306 1 398 Based on company announcements, the global manufacturing capacity for electrolysers couldreach 65 GW per year by 2030. 2023 1 459 1 125 2 933 5 517 2030 - NZE - - - 720 000
GS analysis GS has three scenarios for installed green hydrogen production capacity, in the 2030 timeframe the minimum and maximum coincide with the IEA estimates listed earlier. We will use the IEA numbers as an upper and lower bound, with the idea that the IEA report was written before the IIJA, IRA in the U.S. This likely increases the interest and competitiveness for hydrogen in the U.S. and globally, offering a boost in electrolyzer manufacturing and green hydrogen projects.
Projected Need in H2 Production IEA 134 to 240 GW installed capacity with these numbers likely increasing far beyond these estimates. End of year (2022) analysis had the project pipeline in excess of 300 GW by 2030. These planned projects and required ramp rate up to 700+ GW installed in 2030 to be on track for net zero by 2050. Electrolyzer production and announced production ramp will not meet this demand. Electrolyzer production is booked years in advance, especially true for MW range systems.
A bit more understanding of the potential manufacturing cost reductions? We are primarily chasing the 72% manufacturing costs - Most alkaline-water electrolyzer stack designs are adaptations of older Chloralkali designs. These designs have many individual components, each with their own fabrication supply chains and requiring intricate assembly, often requiring part placement/alignment and unitization to be facilitated by manual labor - Our design eliminates, integrates or combines many of the individual components and greatly simplifies the unitization and stacking process - The design is simplified to the point we believe manufacturing can be automated and scaled with low part handling and manpower requirements even with moving to large area cells at high production rates Alkaline Electrolyzer cost breakdown. Goldman Sachs Carbonomics 2022 12
How much automation is needed for scale? The design, having been simplified and designed from the beginning to allow automation, is what will really drive the cost reduction The automation level will need to be high to realize full cost reduction and peak margin. Early financial models show the product should still be profitable before reaching a high level of automation The required investment for scaled production automation should be low. We are using standard robotics and standard manufacturing techniques with custom tooling. Left: used ABB 6-axis robot landed at the manufacturing facility. ~$25,000 - $30,000 per used robot 13